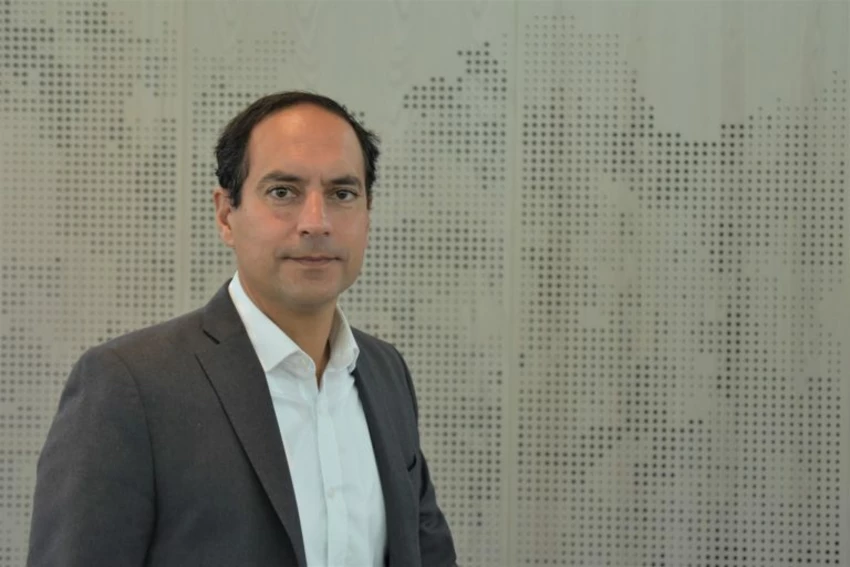
VS: Measures to contain the global COVID-19 outbreak will disrupt trade flows and constrain supply and demand, by keeping people away from work in production, shopping and travelling. How do you expect supply chains to be affected for corporates?
PZ: Systemic supply chain shocks are not a new phenomenon. Earlier incidents include the SARS virus outbreak in 2003-04, the Fukushima nuclear plant accident in Japan after an earthquake in March 2011, and the volcano eruption on Iceland in April 2010, which created an enormous ash cloud and grounded all flights in northern Europe. All of these events stretched supply-chain resilience. It took Toyota three months to get back to pre-earthquake production rates in 2011, and the European land and sea transport network was under enormous pressure for six days to keep supplies flowing.
What has changed over time is the reliance on China in the global economy. Back in 2003 during the SARS outbreak, China accounted for only 4% of global GDP. Today it is 16%. Furthermore, the increased shift towards China in the global supply chain has been driven by cost and competence factors.
Another fundamental change is that China has climbed the value-chain ladder from manufacturing components to also assembling products, and it has become an important trade partner for developing countries. Hence, the ripple-effect from a disruption in China can be sudden and unexpected, such as General Motors’ Louisiana plant closing down owing to a lack of Japanese-made parts after the Fukushima accident. Such disruption will be felt not only in developed countries, but also among manufacturing hubs in developing countries where much needed raw materials are trapped. For example, the vast majority of factories in Bangladesh source raw materials from China.